Any change or assurance initiative benefits from knowing the current baseline of the processes, controls and activities that deliver an outcome; what are the requirements, what needs to be changed, who/what is impacted, what are the issues, risks & costs and what is the gap between current state and the target operating model?
All of these are key pieces of information that need to be captured and understood. However, this analysis takes time, can be confusing and is therefore very hard to scale and get right.
In this paper we will be focusing on how you can improve the Process Mapping process and outcomes from it through Automated Process Modelling.
Process Mapping – the traditional way
Up to recently the only method to capture the detail required to baseline a change initiative has been manual, resource intensive, inaccurate and time consuming, involving; workshops, interviews, observation and examination of multiple stakeholder groups, functions, business units, third party partners, suppliers and geographies. For the same service, there may be multiple process variations and differences in their enablers (People, Technology, Data, Facilities) as well as variations in how work is done by individuals themselves.
Typically, a Process Mapping exercise to capture the above takes the following path:
- Business Analysts and PMO herding subject matter experts (SMEs) from different stakeholder groups, gathering historic information, running workshops, holding interviews, observing and examination of work of many different SMEs,
- Capturing this information in diagram and/or narrative form, usually two-dimensional and in a combination of Visio, Word, Excel and PowerPoint that makes it hard to analyse, maintain and co-ordinate,
- Verifying what has been documented with the stakeholders through follow up workshops, interviews, observation etc. and multiple rework loops of updating the documentation as different and more information comes to light,
- Sign off of the documentation to be used for the initiative (usually a single view – the perceived right way of working),
- Challenge to the signed off documentation,
- Documentation becomes redundant.
The issue with this method is that it is time consuming, hard to coordinate, inaccurate by design and disruptive to the operations of the organisation.
Automated Process Modelling
The aim and benefits
Automated Process Modelling alleviates most of the above issues and enables scalability and consistency of documented processes across an organisation. Through the use of automation processes are captured in an objective manner, which delivers;
- greater accuracy as all variations in ways of working are captured and able to be analysed.
- faster documentation of processes as the process models are captured from existing system data and recording of real time activity.
- less disruption of operational work as the automation works in the background with no impact on the SMEs performing the work.
Due to the above the cost of documenting processes is significantly reduced and the Business Analysts and SMEs are able to focus on higher value tasks gaining deeper insights into the processes and therefore significantly increasing the payback to the organisation through better and more improvements per person delivering potential productivity gains from APM of 75% compared to manual Process Mapping.
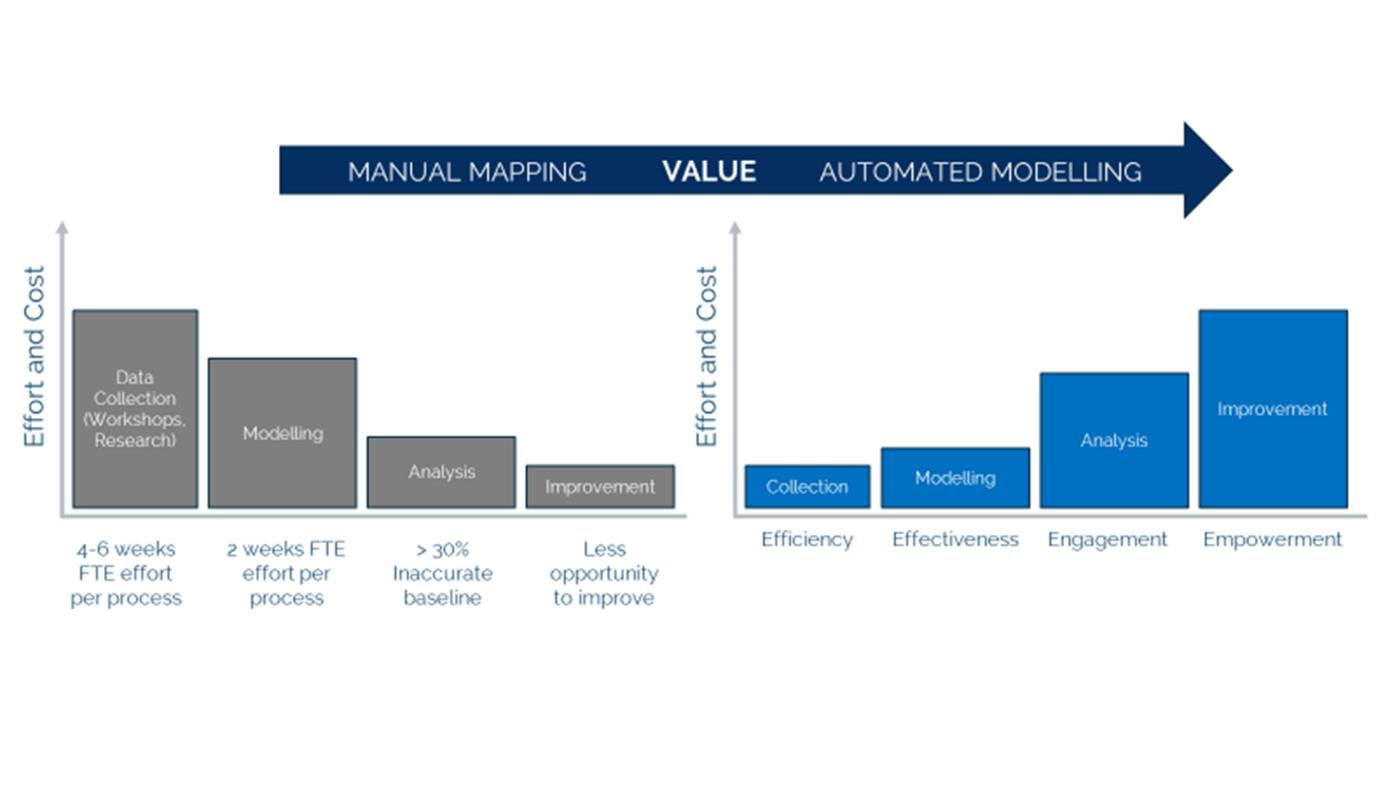
How it works
Automated Process Modelling uses a combination of Process Mining and Task Mining to build up an end-to-end process model which are then visualised in a Business Process Management tool, enabling analysis, monitoring and reporting.
Process Mining uses Event Logs from core business systems such as CRM and ERP applications, using the data from each transaction instance, to build up an end to end process model based on the data points that are captured in the core business systems. As long as there are three key data elements (ID, Activity & Timestamp) the process can be captured and built by the process mining tool. This gives a reasonable level of detail of the process and can be enhanced with additional data points to give enable further analysis and reporting capability. However, in most processes the majority of tasks are done outside of the core systems using desktop or web applications such as e mail, website searches and spreadsheets etc. therefore process mining on its own does not enable a full capture of the end to end process, so by combining the process mining with Task Mining the full end to end process can be captured in detail.
Task Mining (using Robotic Process Discovery) records individual users’ actions (e.g. mouse clicks, scrolling and typing) adding a timestamp and leveraging artificial intelligence to build up detailed processes with all the multiple variants that come with how individuals interact with desktop applications to perform their business tasks. These detailed processes are then knitted into the higher-level end to end process that has been captured by the process mining to give a fully objective, accurate and detailed view of how a process is performed, enabling Business Analysts to spend their time analysing the inefficiencies and identifying the improvement and automation opportunities and creating the designed process in the Business Process Management tool for future compliance monitoring, training and analysis for improvement.
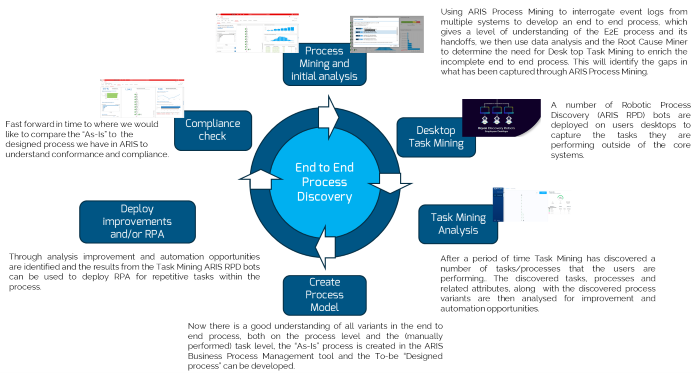
A TYPICAL END TO END APM PROCESS DISCOVERY CYCLE
Conclusion
Digital transformation and automation are, rightly, high on the agenda for many executives. However, transformation has been hampered by the ability to identify the right opportunities for automation (RPA, integration, blockchain, AI, ML, IoT, etc.) and the high cost, complexity and inaccuracy of capturing the processes activities and tasks that need to be automated using traditional process mapping methods.
Now with Automated Process Modelling these barriers have been reduced and businesses are able to focus on delivering outcomes based on objective insights that have been captured accurately, at lower cost and effort than traditional process mapping.
Ownet are able to support you through the full lifecycle of your transformation and assurance programmes, advise on the best tools to support you and offer Mapping as a Service using our Automated Process modelling solution powered by Software AG. For further information on how we can help please contact: Jeremy.James@ownet.co.uk